Pompes
Ce chapitre traitera plus en détail de la pressurisation de l'eau, des deux principales conceptions de pompes utilisées pour ce faire, des parties de la pompe à intensification et du dépannage des fuites dans la pompe à intensification. Le transport et le dosage de l'abrasif seront également couverts.
Courses
Découpe au jet d'eau haute pression
L’eau est pressurisée à des pressions très élevées, supérieures à 50 000 psi. Cette pressurisation est réalisée à l’aide de pompes de conceptions diverses, décrites ci-après dans ce chapitre.
L’eau à haute pression est transportée à travers une série de tubes en acier inoxydable jusqu’à une tête de coupe. Selon le matériau à couper, la tête de coupe peut être soit une « tête de coupe à eau pure » soit une « tête de coupe abrasive ».
Dans la tête de coupe, l’eau à haute pression est forcée à travers un orifice de petit diamètre. Le diamètre de cet orifice est de 0,004″ à 0,020″. Cette étape convertit la pression du jet d’eau en vitesse. On passe de l’énergie potentielle à l’énergie cinétique. En sortant de l’orifice, le jet d’eau se déplace à 2200 mph ou plus. Une pression plus élevée entraîne une vitesse plus élevée. Des orifices de plus petit diamètre produisent un jet d’eau plus rapide, mais aussi un jet avec moins d’énergie cinétique car il n’y a pas autant d’eau disponible pour accélérer les grains abrasifs à pleine vitesse.
Dans une tête de coupe à eau pure, l’eau sort immédiatement de la tête de coupe après avoir traversé l’orifice. La vitesse et la puissance du jet d’eau sont suffisantes pour couper des matériaux mous ou minces comme la mousse, le caoutchouc, le bois tendre, les plastiques, les tapis, les aliments, les garnitures de toit de voiture, les circuits imprimés, etc.
Dans une tête de coupe abrasive, un abrasif très dur, généralement du grenat, est introduit dans le jet d’eau. Les particules abrasives sont accélérées à près de la vitesse du jet d’eau. Cela donne aux particules abrasives beaucoup de puissance. Le jet d’eau abrasif descend maintenant à travers une buse abrasive, ou tube de mélange, d’environ 3 pouces de long avec un diamètre intérieur compris entre 0,030″ et 0,050″. Le mélange d’eau et d’abrasif sort de la buse abrasive et coupe les matériaux durs comme les métaux, la pierre, l’acrylique, la céramique, les composites, les phénoliques et la porcelaine.
Une commande CNC déplacera la tête de coupe jusqu’à 6 axes de mouvement pour couper la pièce à usiner ciblée.
Types de pompes
Intensificateur
Les pompes à intensificateur sont appelées intensificateurs car elles utilisent le concept d’intensification ou d’amplification de la pression pour générer la pression d’eau souhaitée.
Si vous appliquez une pression sur un côté d’un cylindre et que l’autre côté du cylindre a la même surface, la pression de l’autre côté sera la même. Si la surface du plus petit côté est la moitié, alors la pression sur ce côté sera doublée. Généralement, avec les pompes à intensificateur, il y a une différence de 20 fois entre la grande surface (où la pression d’huile est appliquée) et la petite surface (où la pression de l’eau est générée). L’image suivante montre ce concept.
En fin de compte, il doit y avoir une restriction dans le débit d’eau pour que la pression soit générée. Cette restriction est générée par l’orifice de la tête de coupe. La pression est maintenue jusqu’à ce que le diamètre de l’orifice dépasse les limites de débit d’eau de la pompe.
Pour les orifices de très petit diamètre, afin de maintenir la pression, la pompe n’a besoin que de cycler très lentement pour maintenir la pression. Au fur et à mesure que l’orifice s’agrandit, la pompe doit fonctionner plus rapidement pour maintenir la pression et le débit d’eau. Si l’orifice devient trop grand, la pompe essaie de cycler trop vite pour les spécifications de conception. Une situation de « surcourse » est détectée par la commande et la pompe s’arrête avec un message d’erreur.
S’il y a des fuites dans le circuit d’eau entre la pompe et la tête de coupe, cela peut également entraîner une situation de « surcourse » de la pompe. Les fuites volent efficacement l’eau disponible pour aller à la tête de coupe. De la même manière que la mise en place d’un orifice trop grand, la pompe fonctionne plus rapidement pour maintenir la pression jusqu’à ce qu’elle atteigne sa limite.
En règle générale, les intensificateurs fonctionnent à environ 50 à 60 coups par minute lorsqu’ils fonctionnent à pleine capacité.
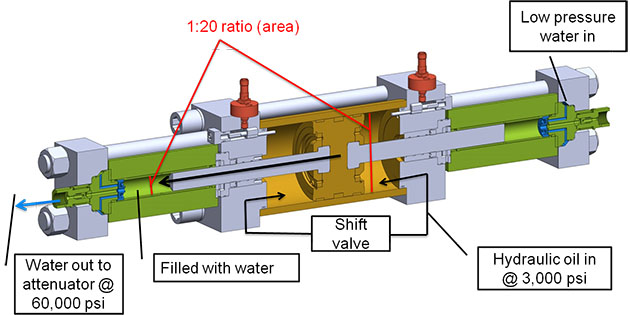
Le processus de pressurisation
- L’huile est forcée dans la moitié droite du vérin hydraulique.
- L’ensemble piston-piston se déplace vers la gauche. L’huile est évacuée de la moitié gauche du vérin hydraulique et l’eau dans le vérin haute pression gauche est mise sous pression.
- Le piston se déplace vers la gauche.
- Une fois que la pression a commencé à monter, l’eau à haute pression est expulsée du multiplicateur par le centre du clapet anti-retour.
- Pendant que l’ensemble piston-piston se déplace vers la gauche, il permet également à l’eau douce de s’écouler dans le cylindre haute pression droit par les trous d’entrée du clapet anti-retour.
- Lorsque l’ensemble plongeur-piston a atteint la fin de sa course vers la gauche, le cylindre haute pression droit est maintenant rempli d’eau.
- La soupape de commande directionnelle reçoit un signal via un capteur de proximité à proximité du piston pour inverser le flux d’huile hydraulique. L’huile est maintenant forcée dans la moitié gauche du cylindre hydraulique et le piston se déplace vers la droite.
- L’huile est déplacée hors de la moitié droite du cylindre hydraulique tandis que l’eau dans le cylindre haute pression droit est pressurisée par le piston droit.
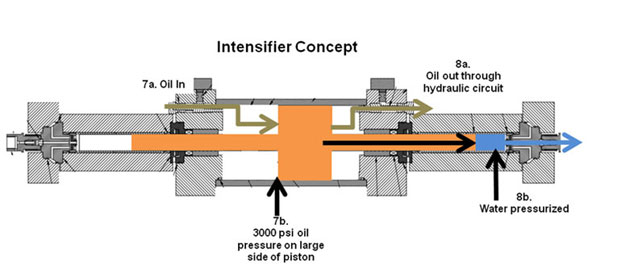
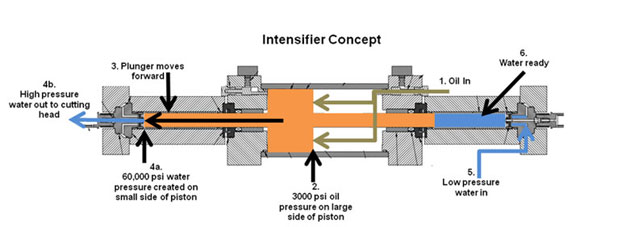
Entraînement direct
Une pompe à entraînement direct fonctionne comme le moteur d’une voiture. Un moteur fait tourner un vilebrequin attaché à 3 pistons décalés ou plus. Lorsque le vilebrequin tourne, les pistons effectuent un mouvement alternatif dans leurs cylindres respectifs, créant une pression dans l’eau. La pression et le débit sont déterminés par la vitesse à laquelle le moteur fait tourner le vilebrequin.
Les pompes à entraînement direct ont un cycle beaucoup plus rapide que les multiplicateurs, de l’ordre de 1750 tours par minute. Les pompes à entraînement direct se trouvent généralement dans des applications à basse pression (c’est-à-dire 55 000 livres par pouce carré et moins). L’entretien de la pompe à entraînement direct a tendance à prendre plus de temps que celui d’une pompe à intensificateur. Les pompes à entraînement direct ne peuvent faire fonctionner plus d’une tête de coupe que si toutes les têtes de coupe coupent la même pièce en même temps. Avec une pompe à intensificateur, vous pouvez avoir des têtes de coupe sur plusieurs machines, couper différentes pièces, activer et désactiver les différentes têtes de coupe dans n’importe quel ordre. La pompe à intensificateur n’aura qu’à faire varier sa vitesse de course en conséquence pour maintenir le débit et la pression.
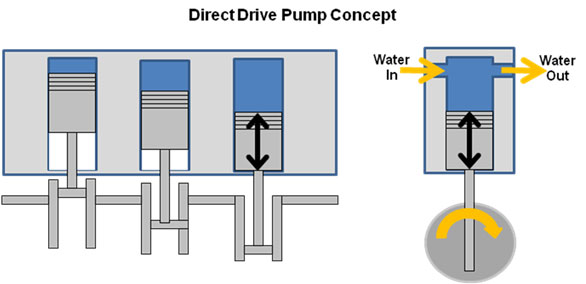
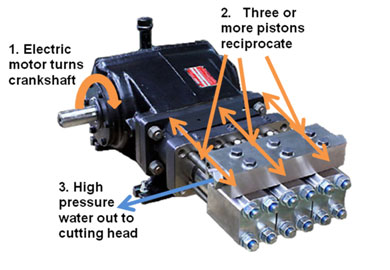
Production d'eau à haute pression : pompes à entraînement direct
- 3 pistons directement couplés à un vilebrequin
- La pression et le débit sont déterminés par la vitesse à laquelle le moteur fait tourner le vilebrequin
- Cycles de vilebrequin jusqu’à 1750 tr/min
- Pics de pression minimes (aucun atténuateur nécessaire)
- Généralement trouvé dans les applications à basse pression
- L’eau de coupe coule toujours lorsque la pompe est en marche. L’eau passe soit par la tête de coupe, soit, lorsqu’elle ne coupe pas, par la soupape de décharge dans le réservoir à jet d’eau.
Désavantages
- Complexe – Nombreuses pièces mobiles
- Temps d’entretien
- Capable de supporter des têtes de coupe supplémentaires UNIQUEMENT lorsque les têtes coupent la même pièce (la pompe est toujours sous pression)
- Cher
Avantages
- Haute efficacité
- Fluctuations de basse pression
- Pas d’atténuateur
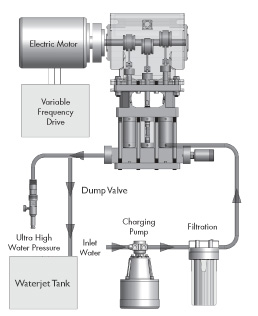
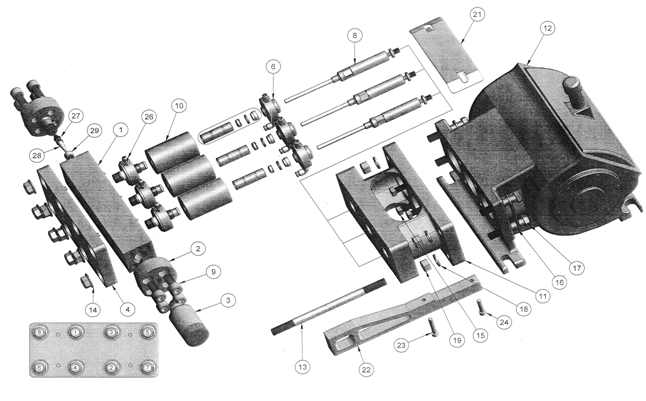
Parties de la pompe à intensificateur
1. Moteur électrique et pompe hydraulique
Le moteur électrique et la pompe hydraulique (numéro 1 sur l’image ci-dessus) créent la pression d’huile nécessaire pour le côté huile de l’intensificateur. Cet ensemble se trouve normalement dans la partie inférieure du boîtier de la pompe. Le moteur électrique et la pompe sont évalués en HP (ou kW pour le système métrique). Les tailles de pompes typiques sont 30 HP, 50 HP, 75 HP, 100 HP et 150 HP Comme indiqué dans le chapitre précédent, chaque pompe aura un volume de sortie d’eau (gallons par minute) et une pression (psi) associés.
Encore une fois, il est important de se rappeler que HP n’est pas nécessairement une indication de pression. Une pompe de 150 CV ne crée pas nécessairement plus de pression qu’une pompe de 50 CV. La puissance est plus directement liée au débit d’eau, car plus de HP seront nécessaires pour créer suffisamment de puissance pour déplacer l’ensemble piston/plongeur dans l’intensificateur à la vitesse de course requise.
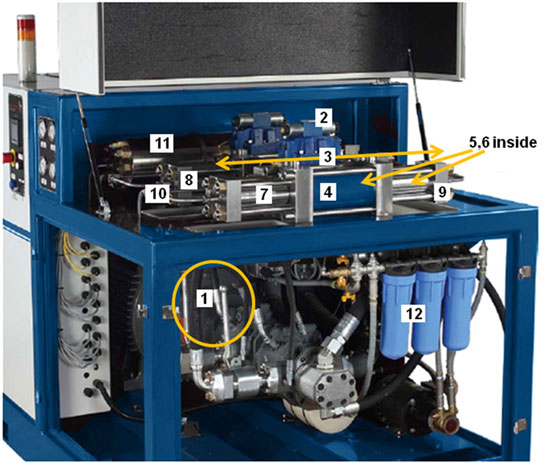
2. Vannes de régulation directionnelles
La vanne de régulation directionnelle (2 sur les figures 2 et 3) contrôle le sens d’écoulement de l’huile hydraulique vers et depuis l’intensificateur.
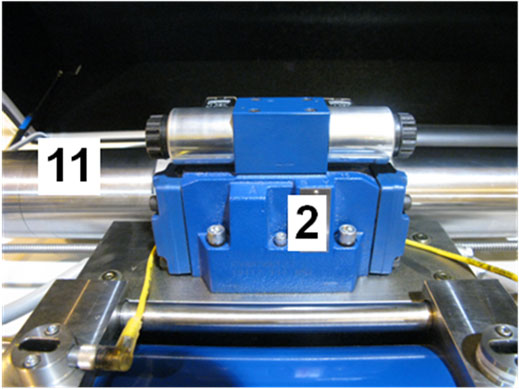
3. Intensificateur
L’intensificateur proprement dit (3 sur les figures 4 et 2) se compose du vérin hydraulique (4), des vérins haute pression (7) et des clapets anti-retour (8) et des embouts (9). Le piston et le plongeur ne sont pas visibles de l’extérieur.
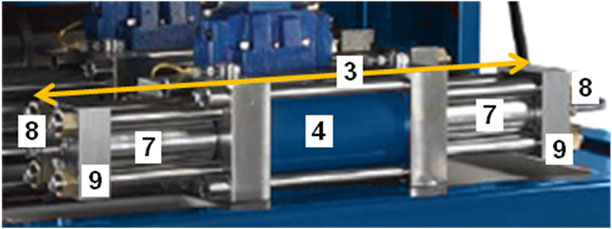
4. Vérin hydraulique
Le cylindre hydraulique (4 sur les figures 2 et 5) abrite le piston et est la zone où l’huile hydraulique fait son travail. Les soupapes de commande directionnelles contrôlent le débit d’huile entrant et sortant de chaque côté du vérin hydraulique.
À chaque extrémité du vérin hydraulique se trouve une plaque d’extrémité qui est utilisée pour connecter le vérin hydraulique au vérin haute pression. Les deux plaques d’extrémité du vérin hydraulique sont reliées et tirées fermement en place avec 4 tirants et boulons.
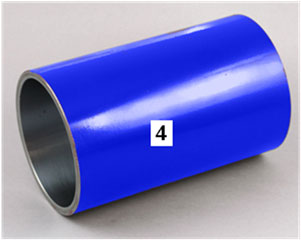
5. Piston
Le piston (numéro 5 sur les figures 2 et 6) est la partie cylindrique de plus grand diamètre située à l’intérieur du vérin hydraulique (4 sur les figures 2 et 5). Le piston divise efficacement le cylindre hydraulique en un côté gauche et un côté droit. L’huile ne peut pas passer d’un côté à l’autre au-delà du piston. Il doit sortir et entrer dans le vérin hydraulique par les tuyaux fixés au distributeur. La pression d’huile hydraulique est exercée de part et d’autre du piston de manière alternée de sorte qu’un mouvement de va-et-vient de l’ensemble piston et plongeur est généré.
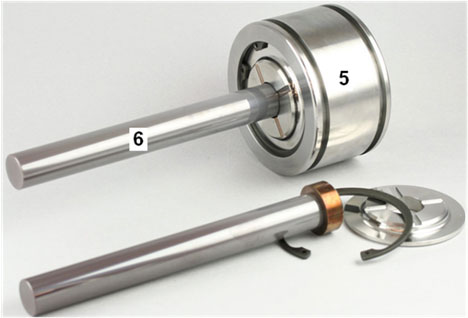
Figure 6 - Ensemble piston (5) et plongeur (6)
6. Plongeur
Les plongeurs (6 sur la figure 7) sont les deux arbres de plus petit diamètre qui sont connectés de chaque côté du piston. Le point de fixation est à l’intérieur du vérin hydraulique. Les autres extrémités des plongeurs s’étendent dans les cylindres haute pression gauche et droit. Des joints sont placés autour de l’arbre du piston pour empêcher l’huile de s’infiltrer dans le côté eau de la pompe, et vice versa. Les pistons sont en acier inoxydable ou, plus récemment, en céramique. La céramique est utilisée en raison de sa capacité à gérer la chaleur et la haute pression avec une faible dilatation thermique.
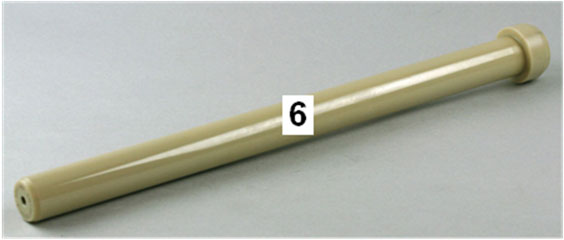
Figure 7 - Plongeur en céramique
7. Cylindre haute pression
Les deux cylindres haute pression (7 sur les figures 8 et 2) sont l’endroit où l’eau est sous pression. Ils sont généralement appelés « côté gauche » et « côté droit ». Les cylindres haute pression sont usinés dans de l’acier inoxydable très épais et traités afin de résister aux pressions extrêmes auxquelles ils sont soumis de façon continue et cyclique.
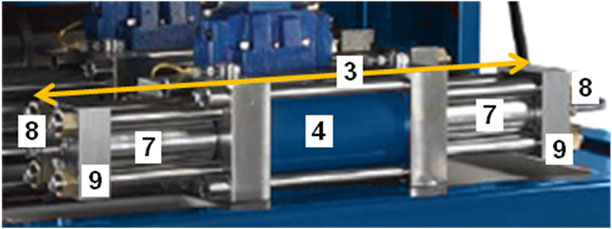
8. Clapet anti-retour
Il y a un clapet anti-retour (numéro 8 sur les figures 10 et 8) à l’extrémité de chaque cylindre haute pression à l’extrémité opposée au cylindre hydraulique. Le clapet anti-retour permet à l’eau douce d’entrer dans le cylindre haute pression et à l’eau haute pression de sortir du multiplicateur. Le clapet anti-retour est conçu pour ne laisser l’eau s’écouler que dans une seule direction. L’eau douce entre par des canaux usinés sur les côtés et sort par un ou plusieurs trous sur la face de la vanne. Divers joints, clapets et sources sont utilisés pour maintenir ce débit d’eau. Au cours de plusieurs centaines d’heures, ces composants s’useront, permettant à l’eau sous pression de s’écouler par le chemin d’admission d’eau, ou permettant à l’eau sous pression de s’infiltrer dans le cylindre haute pression. Les symptômes et le diagnostic de ces différentes situations seront abordés plus loin dans le chapitre « Entretien ».
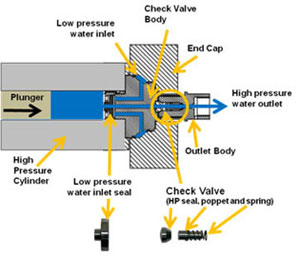
Figure 9 - Coupe transversale du corps du clapet anti-retour
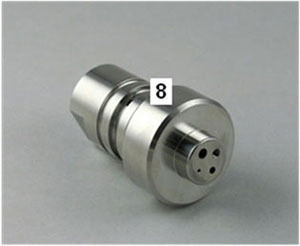
Figure 10 - Corps du clapet anti-retour
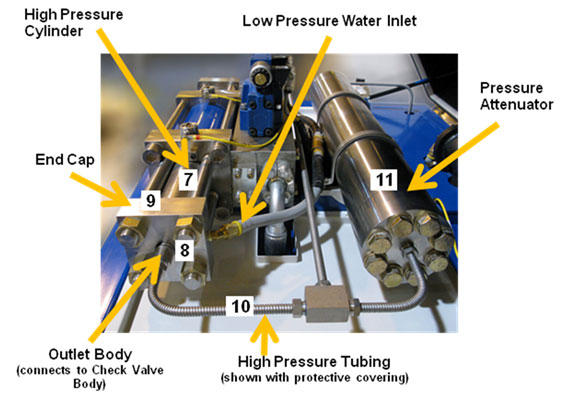
Figure 11 - Vue de la partie supérieure de l'armoire de l'intensificateur
Embout
Le capuchon d’extrémité (numéro 9 sur les figures 11 et 2) est un élément cylindrique ou carré. La version cylindrique se visse sur l’extrémité de sortie du cylindre haute pression. Le type carré est maintenu en place avec des tirants et des boulons. Le capuchon d’extrémité a un trou au centre pour le clapet anti-retour et le corps de sortie. Il disposera également d’un point de raccordement pour l’arrivée d’eau douce. L’eau s’écoule à travers des trous usinés à travers le capuchon pour s’aligner avec les trous d’entrée dans le clapet anti-retour.
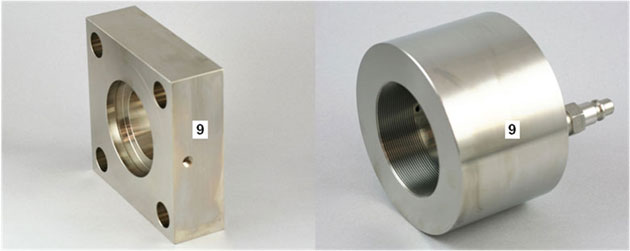
10. Tube haute pression
Un tube en acier inoxydable 304 ou 316 haute pression (numéro 10 sur la figure 11) est fixé à la sortie de chaque clapet anti-retour. Les diamètres extérieurs courants sont de 0,25″, 0,313″, 0,375″ et 0,563″. Les diamètres intérieurs vont de 0,062″ à 0,312″. Il y a généralement un revêtement protecteur souple autour du tube.
Le tube haute pression du cylindre haute pression gauche se joindra à un moment donné au tube haute pression du cylindre droit. Le tube haute pression transporte l’eau sous pression jusqu’à l’atténuateur de pression. Un tube haute pression supplémentaire canalisera l’eau haute pression vers la tête de coupe.
La longueur, le nombre de coudes et d’autres obstacles à l’écoulement (par ex. vannes manuelles) dans le trajet du tube haute pression doivent être pris en considération lors de la conception d’un système de jet d’eau haute pression. La pression chute à chaque coude du tube. De plus, à mesure que la distance entre la pompe et la tête de coupe augmente, la friction interne de l’eau lorsqu’elle traîne contre les parois internes générera de la chaleur entraînant une perte de pression de l’eau. Ce sujet sera abordé plus en détail dans le chapitre 5 « Chute de pression dans les tubes ».
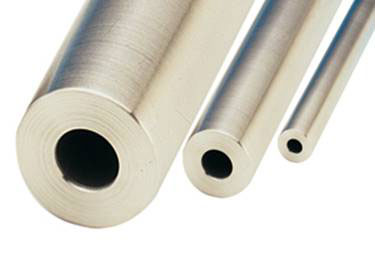
11. Atténuateur de pression
L’atténuateur de pression (numéro 11 sur les figures 13 et 2) atténue les variations de pression après la sortie de l’eau haute pression du multiplicateur. A chaque inversion de cycle de l’intensificateur, il y a un léger retard dans l’augmentation de la pression d’eau dans le cylindre haute pression opposé. Ce retard est dû à : 1) inversion du mouvement où la vitesse instantanée à la fin de la course est égale à zéro, et 2) retards mécaniques d’inversion. Tous ces facteurs peuvent entraîner une baisse de la pression de l’eau. Certains fabricants utilisent une technologie exclusive pour réduire cette chute de pression, que nous vous suggérons d’étudier lors de la sélection d’une pompe. En règle générale, si une pompe de 50 HP peut supporter un orifice de 0,014″ à une pression de fonctionnement continue de 60 000 psi, cela implique que ce défi de perte de charge hydraulique aura été résolu.
L’atténuateur de pression (numéro 11 sur les figures 13 et 2) atténue les variations de pression après la sortie de l’eau haute pression du multiplicateur. A chaque inversion de cycle de l’intensificateur, il y a un léger retard dans l’augmentation de la pression d’eau dans le cylindre haute pression opposé. Ce retard est dû à : 1) inversion du mouvement où la vitesse instantanée à la fin de la course est égale à zéro, et 2) retards mécaniques d’inversion. Tous ces facteurs peuvent entraîner une baisse de la pression de l’eau. Certains fabricants utilisent une technologie exclusive pour réduire cette chute de pression, que nous vous suggérons d’étudier lors de la sélection d’une pompe. En règle générale, si une pompe de 50 HP peut supporter un orifice de 0,014″ à une pression de fonctionnement continue de 60 000 psi, cela implique que ce défi de perte de charge hydraulique aura été résolu.
La figure 14 montre les fluctuations de pression dans la conduite d’eau haute pression avant l’accumulateur de pression. Cela montre un changement de pression de haut en bas de près de 22 000 psi. Ainsi, pour un système à 60 000 psi, l’eau à haute pression passerait de 60 000 psi à 40 000 psi après chaque coup de l’intensificateur.
Si cette fluctuation de pression n’était pas lissée par l’atténuateur de pression, les résultats de coupe au niveau de la pièce à usiner seraient indésirables. Il y aurait une ligne significative dans la pièce à chaque coup de l’intensificateur. Rappelons que tout changement de pression entraîne un changement de vitesse du jet d’eau au niveau de la tête de coupe. Ce changement de vitesse modifie la vitesse à laquelle les particules abrasives se déplacent et, par conséquent, la quantité de force qu’elles transmettront à la pièce à usiner. Une pression plus basse entraîne une vitesse de l’eau moindre, ce qui entraîne une force moindre de l’abrasif, ce qui entraîne une coupe plus lente ou une qualité de bord plus rugueuse.
Heureusement, l’atténuateur de pression atténue ces pics de pression afin que l’eau à la tête de coupe maintienne une pression, une vitesse et une puissance de coupe constantes.
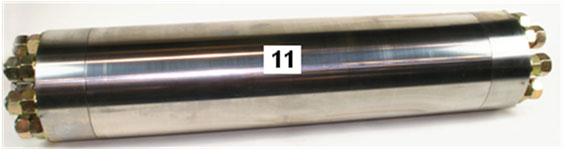
Figure 13 - Atténuateur de pression
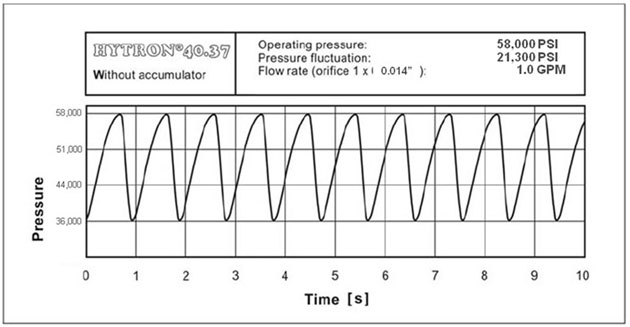
Figure 14 - Fluctuation de la pression avant l'accumulateur
Source : " Fluctuations de la pression et du débit dans les pompes à intensification de haute pression ", F. Trieb, et.al., 2007 American WJTA Conference and Expo
12. Entrée d'eau
Avant d’entrer dans l’armoire de la pompe, l’eau peut devoir être traitée pour obtenir l’eau conforme aux spécifications du fabricant du jet d’eau. Dans l’armoire de la pompe, généralement dans la partie inférieure, l’eau passera généralement par un ou plusieurs filtres finaux juste avant d’entrer dans l’intensificateur (numéro 12 sur les figures 15 et 2).
L’eau d’entrée doit être capable de maintenir un débit et une pression spécifiés pour s’assurer que le multiplicateur reçoive suffisamment d’eau. L’eau entrante doit également répondre à certaines exigences en ce qui concerne les solides dissous totaux (TDS), le pH, la matière organique, la température, etc. Une eau de mauvaise qualité réduira considérablement la durée de vie des composants haute pression (c’est-à-dire tout ce avec quoi l’eau haute pression entre en contact). Différents fabricants de pompes exigent différentes pressions d’eau d’entrée, certains n’ayant besoin que de 30 psi, et d’autres exigeant une pompe de surpression d’eau pour maintenir 100 psi. La qualité de l’eau sera discutée plus en détail dans le chapitre 4 « Qualité de l’eau ».
Figure 15 - Filtres à eau d'entrée
13. Contrôles et API
Les commandes et le PLC (non illustrés) contrôlent les vannes du circuit hydraulique pour déterminer la pression et le débit de l’huile hydraulique vers et depuis l’intensificateur. Divers capteurs et interrupteurs de proximité peuvent également être intégrés aux commandes pour surveiller l’ensemble de la pompe afin de vérifier des éléments tels que le taux de course, la température et la pression de l’huile, la pression et le débit d’eau d’entrée, etc. Cette capacité facilite grandement l’utilisation et le dépannage de l’intensificateur moderne.
La vanne pneumatique On-Off contrôle le débit d’eau vers la tête de coupe. La vanne On-Off au niveau de la coupe est « normalement fermée ». C’est-à-dire que lorsqu’il n’y a pas d’air comprimé fourni à la vanne marche-arrêt, une aiguille s’ajuste étroitement contre un siège pour empêcher toute eau à haute pression d’atteindre la tête de coupe. Lorsque de l’air comprimé est fourni à la vanne marche-arrêt (c’est-à-dire la commande « outil en marche » de la commande), l’aiguille est forcée de son emplacement d’assise et l’eau à haute pression peut s’écouler à travers l’orifice vers la tête de coupe.
À l’intérieur ou à proximité de l’armoire de la pompe haute pression se trouve une autre vanne marche-arrêt qui fonctionne en tandem avec la vanne marche-arrêt de la tête de coupe. La vanne tout ou rien de la pompe est généralement appelée soupape de décharge de sécurité. Cette soupape de sûreté de la pompe est « normalement ouverte ». Cette vanne reste ouverte lorsqu’il n’y a pas d’air qui lui est fourni. Lorsque la vanne marche-arrêt de la tête de coupe se ferme (commande « d’arrêt de l’outil » par contrôle ou pas d’alimentation du système), la soupape de sécurité de la pompe s’ouvre, libérant toute la pression de l’eau du tube haute pression. Lorsque la commande « outil en marche » est émise par la commande, la soupape de sécurité se ferme afin que toute l’eau à haute pression aille à la tête de coupe. Notez que tous les fabricants de pompes neuves n’ont pas la soupape de décharge de sécurité en standard. Nous vous suggérons fortement de demander à votre fabricant de pompe s’il fournit cette norme et quand elle est activée. Encore une fois, certains fabricants de pompes n’activent la soupape de sécurité que lorsqu’un arrêt d’urgence est enfoncé ; lorsque la pompe s’arrête, les conduites haute pression sont toujours sous pression.
Ces deux vannes tout ou rien doivent être en bon état de fonctionnement pour protéger contre les décharges accidentelles d’eau à haute pression au niveau de la tête de coupe qui pourraient gravement blesser quelqu’un travaillant sur ou à proximité de la tête de coupe ou de l’une des conduites à haute pression. Le remplacement périodique du pointeau, du siège et des pièces associées est nécessaire pour maintenir ces vannes.
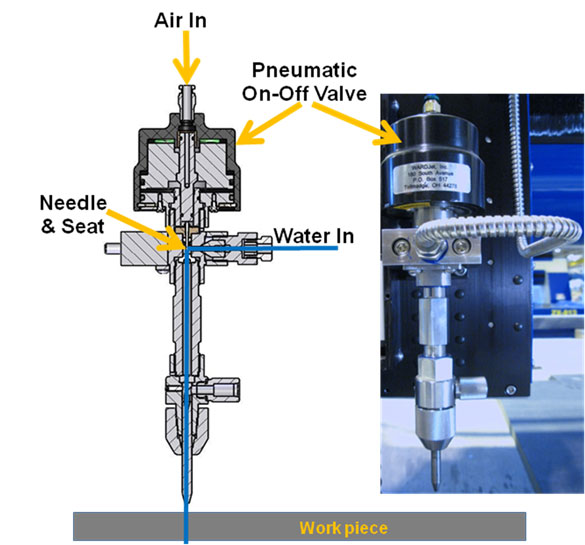
Système d'alimentation en abrasif
Trémie en vrac sous pression
L’abrasif est transporté via des tubes et sous pression d’une grande trémie en vrac située près du système de découpe au jet d’eau à une mini-trémie près de la tête de coupe. Les trémies en vrac contiendront normalement de plusieurs centaines de livres d’abrasif à 2200 livres. Si vous coupez avec une tête et 1,4 livre par minute d’abrasif, vous consommez environ 84 livres par heure. Une trémie de 1100 livres durerait environ 13 heures de fonctionnement. Cela signifierait que la machine pourrait fonctionner pendant bien plus d’un quart de travail avant de devoir être rechargée. La plupart des jets d’eau sont équipés de trémies d’environ 600 livres, ce qui équivaudrait à environ 7 heures de fonctionnement. Ainsi, au moins une fois pendant un quart de travail de 8 heures, la trémie devrait être rechargée. Les coûts associés aux temps d’arrêt supplémentaires au cours d’une année doivent être évalués.
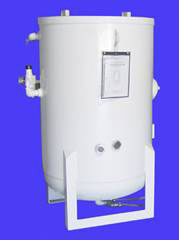
Mini trémie
Une mini-trémie est généralement montée à proximité et au-dessus de la tête de coupe. La plupart de ces mini-trémies permettent une alimentation par gravité de l’abrasif jusqu’à la tête de coupe. De nombreuses mini-trémies contrôlent la quantité d’abrasif qui peut descendre jusqu’à la tête de coupe à l’aide d’une glissière avec des trous de différentes tailles. L’opérateur peut modifier la position de la glissière pour modifier la quantité d’abrasif vers la tête de coupe.
Une avancée technologique récente est le contrôle CNC à distance de la quantité d’abrasif libéré de la mini-trémie. Cette capacité permet une alimentation optimale de l’abrasif à la tête de coupe par rapport à la pression de l’eau à la pompe pour les capacités souhaitables suivantes :
- Perçage de matériaux fragiles comme le verre ou la pierre. En règle générale, une pression d’eau inférieure sera utilisée avec une plus petite quantité d’abrasif
- Modification de la quantité d’abrasif pour différentes tailles de buses abrasives afin d’optimiser le coût des pièces. Cela peut être fait automatiquement si la mini trémie est configurée pour cela.
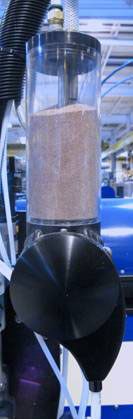
Sommaire
Dans ce chapitre, après un bref examen du processus de découpe au jet d’eau, nous avons examiné les deux pompes de style différent utilisées dans la découpe au jet d’eau à haute pression : l’intensificateur et l’entraînement direct, et nous avons couvert quelques-uns des avantages de chaque style de pompe. Le processus de pressurisation de l’eau d’une pompe multiplicatrice a été détaillé. Nous avons passé en revue les différentes parties d’une pompe multiplicatrice afin que vous ayez une bonne idée de ce dont parle un vendeur ou un technicien lorsqu’il fait référence à une partie d’une pompe. Nous avons également discuté de la vanne On-Off et de son utilisation au niveau de la tête de coupe et de la pompe. Le système d’alimentation en abrasif a été discuté, ainsi que les mérites d’un système de dosage d’abrasif contrôlé par CNC.
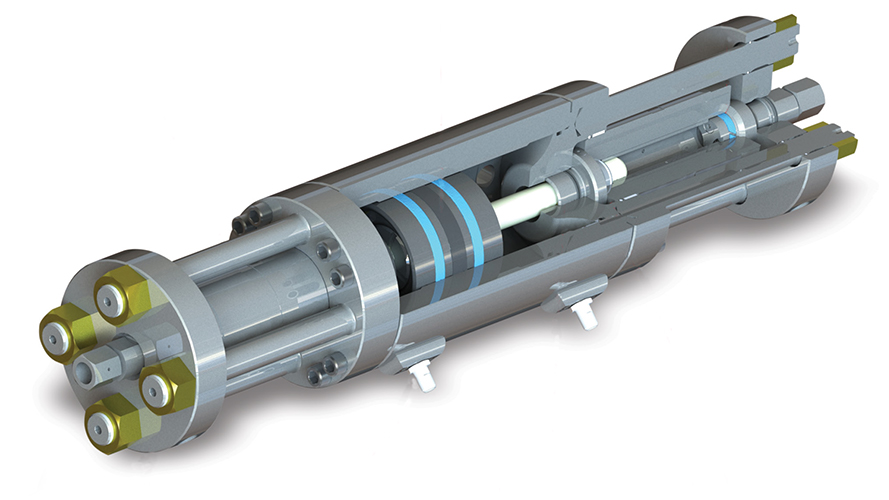














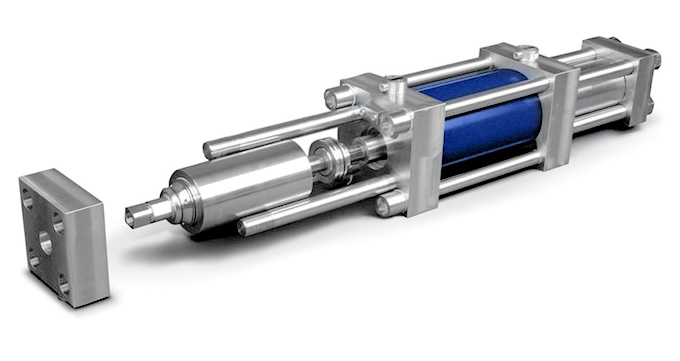












Entrer en contact
Joignez-vous à notre équipe
Nous sommes toujours à la recherche de personnes compétentes et passionnées par l'offre d'une expérience client exceptionnelle. Parlons!