Bombas de Agua
Este capítulo discutirá la presurización del agua con más detalle, los dos diseños de bombas principales que se utilizan para hacer esto, las partes de la bomba intensificadora y la resolución de problemas de fugas en la bomba intensificadora. También se cubrirán el transporte y la dosificación de abrasivos.
Courses
Corte por chorro de agua a alta presión
El agua se presuriza a presiones muy altas, superiores a 50.000 psi. Esta presurización se logra con el uso de bombas de varios diseños, que se describen a continuación en este capítulo.
El agua a alta presión se transporta a través de una serie de tubos de acero inoxidable hasta un cabezal de corte. Dependiendo del material que se corte, el cabezal de corte puede ser un «cabezal de corte de agua pura» o un «cabezal de corte abrasivo».
En el cabezal de corte, el agua a alta presión se fuerza a través de un orificio de pequeño diámetro. El diámetro de este orificio oscila entre 0,004 «y 0,020». Este paso convierte la presión del chorro de agua en velocidad. Pasamos de la energía potencial a la energía cinética. Al salir del orificio, la corriente de chorro de agua se mueve a 2200 mph o más rápido. Una presión más alta da como resultado una velocidad más alta. Los orificios de menor diámetro producen una corriente de chorro de agua más rápida, pero también una corriente con menos energía cinética, ya que no hay tanta agua disponible para acelerar los granos abrasivos a la velocidad máxima.
En un cabezal de corte de agua pura, el agua sale inmediatamente del cabezal de corte después de pasar por el orificio. La velocidad y la potencia del chorro de agua es suficiente para cortar materiales blandos o delgados como espuma, caucho, madera blanda, plásticos, alfombras, alimentos, techos de automóviles, placas de circuitos y más.
En un cabezal de corte abrasivo, se alimenta un abrasivo muy duro, típicamente granate, a la corriente de chorro de agua. Las partículas abrasivas se aceleran hasta cerca de la velocidad del chorro de agua. Esto le da a las partículas abrasivas mucho poder. La corriente de chorro de agua abrasiva ahora viaja hacia abajo a través de una boquilla abrasiva, o tubo de mezcla, de aproximadamente 3 pulgadas de largo con un diámetro interno de entre 0,030 «y 0,050». La mezcla de agua y abrasivo sale de la boquilla abrasiva y cortará materiales duros como metales, piedra, acrílico, cerámica, compuestos, fenólicos y porcelana.
Un control CNC moverá el cabezal de corte en hasta 6 ejes de movimiento para cortar la pieza de trabajo objetivo.
Tipos de bombas
Intensificador
Las bombas intensificadoras se denominan intensificadores porque utilizan el concepto de intensificación o amplificación de la presión para generar la presión de agua deseada.
Si aplica presión a un lado de un cilindro y el otro lado del cilindro tiene la misma superficie, la presión en el otro lado será la misma. Si el área de la superficie del lado más pequeño es la mitad, entonces la presión en ese lado se duplicará. Generalmente, con las bombas intensificadoras hay una diferencia de 20 veces entre el área de superficie grande (donde se aplica la presión del aceite) y el área de superficie pequeña (donde se genera la presión del agua). La siguiente imagen muestra este concepto.
En última instancia, debe haber una restricción en el flujo de agua para que se genere la presión. Esta restricción es generada por el orificio en el cabezal de corte. La presión se mantiene hasta que el diámetro del orificio excede los límites de salida de agua de la bomba.
Para orificios de diámetro muy pequeño, para mantener la presión, la bomba solo necesita realizar un ciclo muy lento para mantener la presión. A medida que el orificio se hace más grande, la bomba debe funcionar más rápido para mantener la presión y el flujo de agua. Si el orificio se vuelve demasiado grande, la bomba intenta realizar un ciclo demasiado rápido para la especificación de diseño. El control detecta una situación de «carrera excesiva» y la bomba se detiene con un mensaje de error.
Si hay fugas en el circuito de agua entre la bomba y el cabezal de corte, esto también puede resultar en una situación de «carrera excesiva» de la bomba. Las fugas roban efectivamente el agua disponible para ir al cabezal de corte. Al igual que colocar un orificio demasiado grande, la bomba funciona más rápido para mantener la presión hasta que alcanza su límite.
Por lo general, los intensificadores golpean alrededor de 50 a 60 golpes por minuto cuando trabajan a plena capacidad.
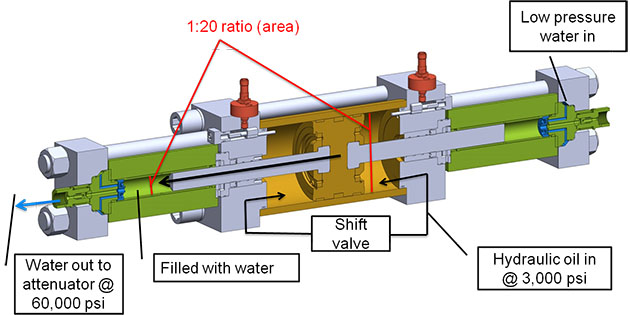
El proceso de presurización
- El aceite entra en la mitad derecha del cilindro hidráulico.
- El conjunto de pistón-émbolo se mueve hacia la izquierda. El aceite se desplaza fuera de la mitad izquierda del cilindro hidráulico y el agua en el cilindro de alta presión izquierdo se presuriza.
- El émbolo se mueve hacia la izquierda.
- Una vez que la presión ha comenzado a acumularse, el agua a alta presión se expulsa del intensificador a través del centro de la válvula de retención.
- Mientras que el conjunto de pistón y émbolo se mueve hacia la izquierda, también permite que fluya agua dulce hacia el cilindro de alta presión derecho a través de los orificios de entrada de la válvula de retención.
- Cuando el conjunto de émbolo-pistón ha llegado al final de su carrera hacia la izquierda, el cilindro de alta presión derecho ahora está lleno de agua.
- La válvula de control direccional recibe una señal a través de un sensor de proximidad cerca del pistón para invertir el flujo de aceite hidráulico. Ahora se fuerza aceite en la mitad izquierda del cilindro hidráulico y el pistón se mueve hacia la derecha.
- El aceite se desplaza fuera de la mitad derecha del cilindro hidráulico mientras que el agua en el cilindro de alta presión derecho es presurizada por el émbolo derecho.
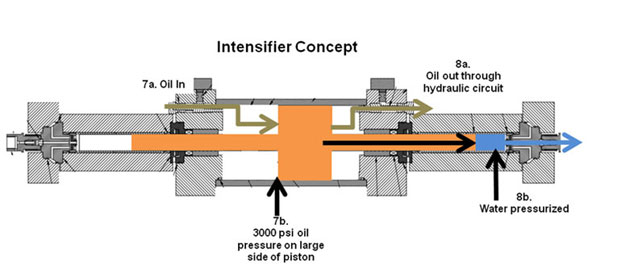
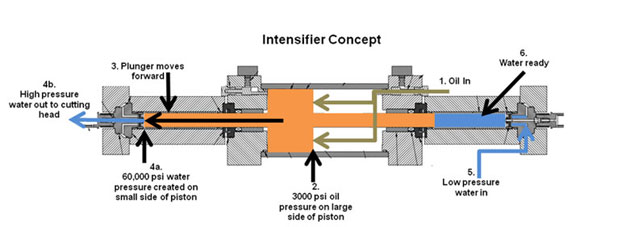
Manejo directo
Una bomba de transmisión directa funciona como el motor de un automóvil. Un motor hace girar un cigüeñal conectado a 3 o más pistones descentrados. A medida que gira el cigüeñal, los pistones se mueven alternativamente en sus respectivos cilindros, creando presión en el agua. La presión y el caudal están determinados por la rapidez con la que el motor hace girar el cigüeñal.
Las bombas de accionamiento directo tienen un ciclo mucho más rápido que los intensificadores, del orden de 1750 revoluciones por minuto. Las bombas de accionamiento directo generalmente se encuentran en aplicaciones de baja presión (es decir, 55,000 libras por pulgada cuadrada y menos). El mantenimiento de la bomba de accionamiento directo suele llevar más tiempo que el de una bomba intensificadora. Las bombas de accionamiento directo solo pueden hacer funcionar más de un cabezal de corte solo si todos los cabezales de corte están cortando la misma pieza al mismo tiempo. Con una bomba intensificadora, podría tener cabezales de corte en varias máquinas, cortando diferentes piezas, activando y apagando los distintos cabezales de corte en cualquier secuencia. La bomba intensificadora solo necesitará variar su frecuencia de carrera en consecuencia para mantener el flujo y la presión.
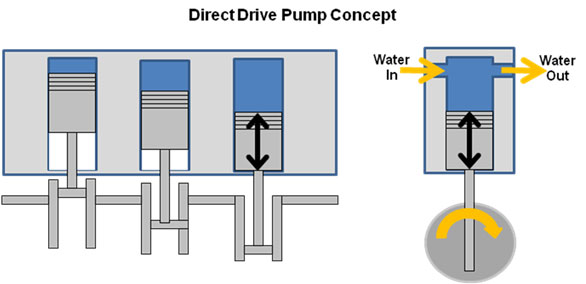
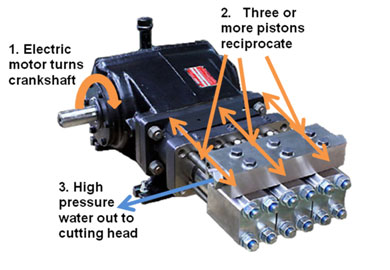
Generación de agua a alta presión: bombas de accionamiento directo
- 3 émbolos acoplados directamente a un cigüeñal
- La presión y el caudal están determinados por la rapidez con la que el motor hace girar el cigüeñal.
- Ciclos del cigüeñal a hasta 1750 rpm
- Picos de presión mínimos (no se necesita atenuador)
- Generalmente se encuentra en aplicaciones de baja presión
- El agua de corte siempre está funcionando mientras la bomba está encendida. El agua pasa a través del cabezal de corte o, cuando no está cortando, a través de la válvula de descarga al tanque de chorro de agua.
Desventajas
- Complejo: muchas partes móviles
- Lleva mucho tiempo mantener
- Capaz de soportar cabezales de corte adicionales SOLO cuando los cabezales están cortando la misma parte (la bomba siempre está presurizada)
- Costoso
Ventajas
- Alta eficiencia
- Fluctuaciones de baja presión
- Sin atenuador
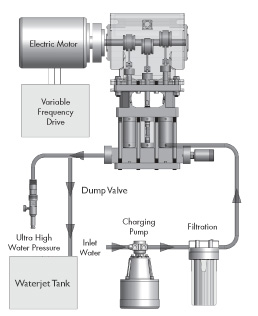
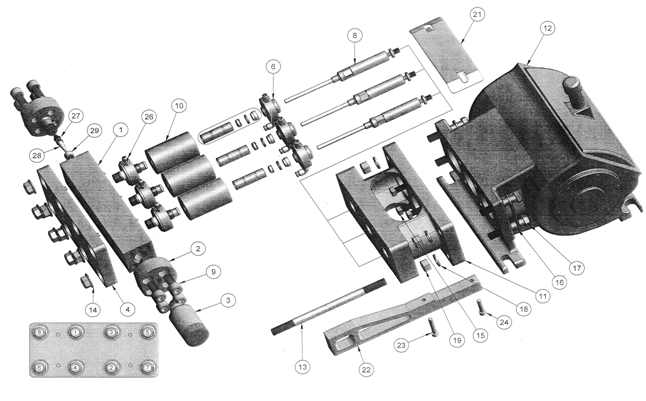
Partes de la bomba intensificadora
1. Motor eléctrico y bomba hidráulica
El motor eléctrico y la bomba hidráulica (número 1 en la imagen de arriba) crean la presión de aceite necesaria para el lado de aceite del intensificador. Este conjunto se encuentra normalmente en la parte inferior del gabinete de la bomba. El motor eléctrico y la bomba están clasificados en HP (o kW para el sistema métrico). Los tamaños típicos de las bombas son 30 HP, 50 HP, 75 HP, 100 HP y 150 HP Como se discutió en el capítulo anterior, cada bomba tendrá un volumen de salida de agua asociado (galones por minuto) y una presión (psi).
Nuevamente, es importante recordar que HP no es necesariamente una indicación de presión. Una bomba de 150 HP no crea necesariamente más presión que una bomba de 50 HP. La potencia está más directamente relacionada con la producción de agua, ya que se necesitarán más HP para crear suficiente potencia para mover el conjunto de pistón / émbolo en el intensificador a la velocidad de carrera requerida.
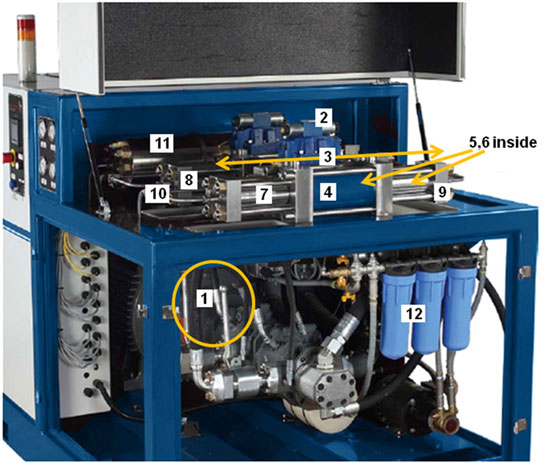
2. Válvulas de control direccional
La válvula de control direccional (2 en las Figuras 2 y 3) controla la dirección de flujo del aceite hidráulico hacia y desde el intensificador.
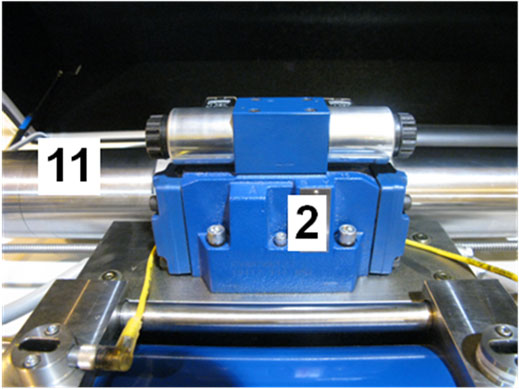
3. Intensificador
El intensificador propiamente dicho (3 en las Figuras 4 y 2) consta del cilindro hidráulico (4), los cilindros de alta presión (7) y las válvulas de retención (8) y las tapas de los extremos (9). No son visibles desde el exterior el pistón y el émbolo.
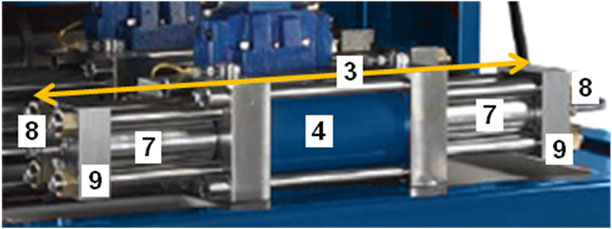
4. Cilindro hidráulico
El cilindro hidráulico (4 en las Figuras 2 y 5) aloja el pistón y es el área donde el aceite hidráulico hace su trabajo. Las válvulas de control direccional controlan el flujo de aceite que entra y sale de cada lado del cilindro hidráulico.
En cada extremo del cilindro hidráulico hay una placa de extremo que se utiliza para conectar el cilindro hidráulico al cilindro de alta presión. Las dos placas de extremo del cilindro hidráulico están conectadas y colocadas firmemente en su lugar con 4 tirantes y pernos.
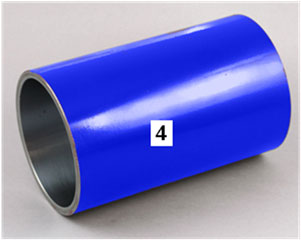
5. Pistón
El pistón (número 5 en las Figuras 2 y 6) es la parte cilíndrica de mayor diámetro ubicada dentro del cilindro hidráulico (4 en las Figuras 2 y 5). El pistón divide efectivamente el cilindro hidráulico en un lado izquierdo y un lado derecho. El aceite no puede pasar de un lado a otro más allá del pistón. Debe salir y entrar en el cilindro hidráulico a través de las mangueras conectadas a la válvula de control direccional. La presión del aceite hidráulico se ejerce sobre cada lado del pistón de forma alterna, de modo que se genera un movimiento hacia adelante y hacia atrás del conjunto de pistón y émbolo.
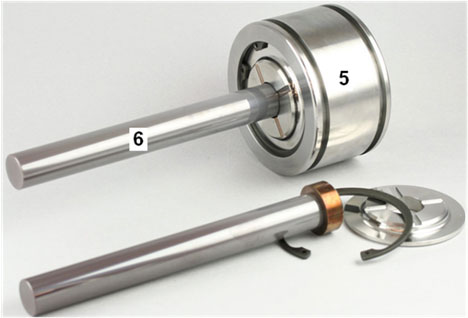
Figura 6 - Conjunto de pistón (5) y émbolo (6)
6. Émbolo
Los émbolos (6 en la Figura 7) son los dos ejes de menor diámetro que están conectados a cada lado del pistón. El punto de enganche está dentro del cilindro hidráulico. Los otros extremos de los émbolos se extienden hacia los cilindros de alta presión izquierdo y derecho. Los sellos se colocan alrededor del eje del émbolo para evitar que el aceite se filtre en el lado del agua de la bomba y viceversa. Los émbolos están hechos de acero inoxidable o, más recientemente, de cerámica. Se utiliza cerámica debido a su capacidad para manejar el calor y la alta presión con poca expansión térmica.
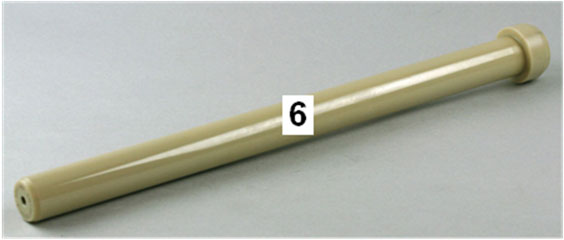
Figura 7 - Émbolo de cerámica
7. Cilindro de alta presión
Los dos cilindros de alta presión (7 en las Figuras 8 y 2) son donde se presuriza el agua. Por lo general, se denominan «lado izquierdo» y «lado derecho». Los cilindros de alta presión están mecanizados en acero inoxidable de gran espesor y tratados para resistir las presiones extremas a las que son sometidos de forma cíclica continua.
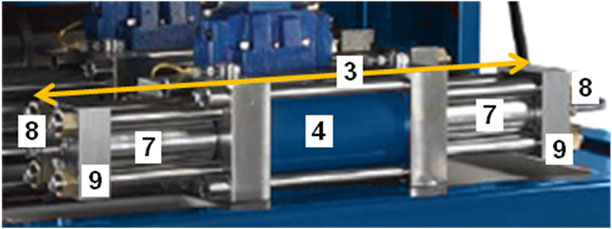
8. Válvula de retención
Hay una válvula de retención (número 8 en las Figuras 10 y 8) al final de cada cilindro de alta presión en el extremo opuesto al cilindro hidráulico. La válvula de retención permite que el agua dulce entre en el cilindro de alta presión y que el agua a alta presión salga del intensificador. La válvula de retención está diseñada para permitir que el agua fluya solo en una dirección. El agua dulce entra a través de canales maquinados en los lados y sale a través de uno o más orificios en la cara de la válvula. Se utilizan varios sellos, poppets y manantiales para mantener este flujo de agua. Durante varios cientos de horas, estos componentes se desgastarán, lo que permitirá que el agua presurizada fluya por la ruta de entrada de agua o que el agua presurizada se filtre nuevamente en el cilindro de alta presión. Los síntomas y el diagnóstico de estas diversas situaciones se discutirán más adelante en el capítulo «Mantenimiento».
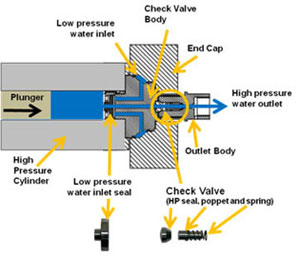
Figura 9 - Sección transversal del cuerpo de la válvula de retención
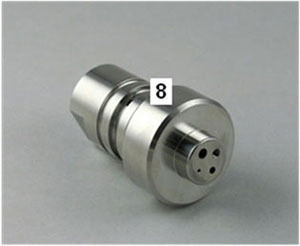
Figura 10 - Cuerpo de la válvula de retención
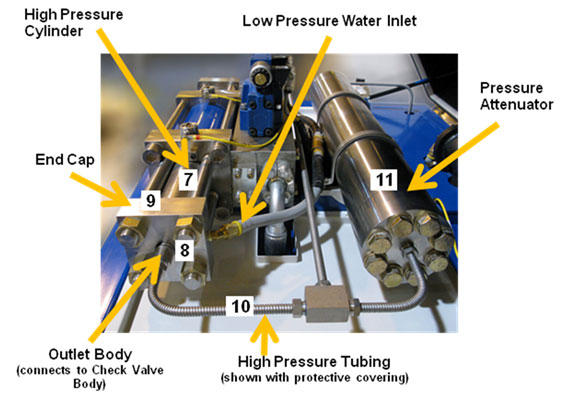
Figura 11 - Vista de la parte superior del gabinete intensificador
Tapa final
La tapa del extremo (número 9 en las Figuras 11 y 2) es un elemento cilíndrico o cuadrado. La versión cilíndrica se atornilla en el extremo de salida del cilindro de alta presión. El tipo cuadrado se mantiene en su lugar con tirantes y pernos. La tapa del extremo tiene un orificio en el centro para la válvula de retención y el cuerpo de salida. También tendrá un punto de conexión para el agua dulce entrante. El agua fluye a través de los orificios maquinados a través de la tapa para alinearse con los orificios de entrada en la válvula de retención.
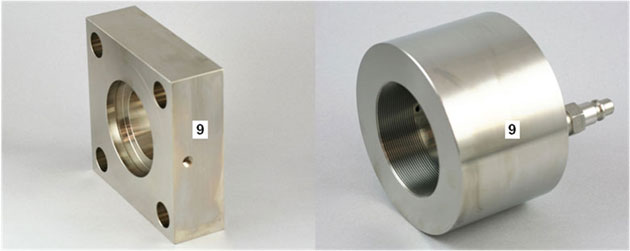
10. Tubería de alta presión
La tubería de acero inoxidable 304 o 316 de alta presión (número 10 en la Figura 11) se conecta a la salida de cada válvula de retención. Los diámetros exteriores comunes son 0.25 «, 0.313», 0.375 «y 0.563». Los diámetros internos varían de 0.062 «a 0.312». Por lo general, hay una cubierta protectora flexible alrededor del tubo.
La tubería de alta presión del cilindro de alta presión del lado izquierdo se unirá en algún punto con la tubería de alta presión del cilindro de la derecha. El tubo de alta presión lleva el agua presurizada al atenuador de presión. Un tubo de alta presión adicional canalizará el agua a alta presión hacia el cabezal de corte.
La longitud, el número de curvas y otras obstrucciones para el flujo (por ejemplo, válvulas manuales) en la trayectoria de la tubería de alta presión deben tenerse en cuenta al diseñar un sistema de chorro de agua a alta presión. La presión caerá con cada doblez del tubo. Además, a medida que aumenta la distancia entre la bomba y el cabezal de corte, la fricción interna del agua a medida que se arrastra contra las paredes internas generará calor, lo que provocará una pérdida de presión del agua. Este tema se discutirá con más detalle en el Capítulo 5 «Caída de presión en la tubería».
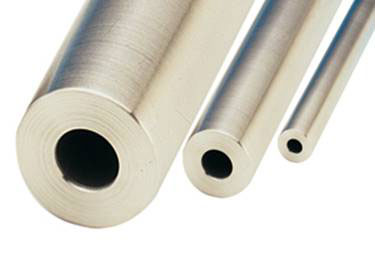
11. Atenuador de presión
El atenuador de presión (número 11 en las Figuras 13 y 2) suaviza las variaciones de presión después de que el agua a alta presión ha salido del intensificador. Con cada inversión de ciclo del intensificador, hay un ligero retraso en el aumento de la presión del agua en el cilindro de alta presión opuesto. Este retraso se debe a: 1) inversión de movimiento donde la velocidad instantánea al final de la carrera es igual a cero, y 2) retrasos mecánicos de inversión. Todos estos factores pueden provocar una caída en la presión del agua. Algunos fabricantes utilizan tecnología patentada para reducir esta caída de presión, que le sugerimos que investigue al seleccionar una bomba. Generalmente, si una bomba de 50 HP puede sostener un orificio de 0.014 «a una presión de operación continua de 60,000 psi, la implicación es que se habrá abordado este desafío de caída de presión hidráulica.
El atenuador de presión (número 11 en las Figuras 13 y 2) suaviza las variaciones de presión después de que el agua a alta presión ha salido del intensificador. Con cada inversión de ciclo del intensificador, hay un ligero retraso en el aumento de la presión del agua en el cilindro de alta presión opuesto. Este retraso se debe a: 1) inversión de movimiento donde la velocidad instantánea al final de la carrera es igual a cero, y 2) retrasos mecánicos de inversión. Todos estos factores pueden provocar una caída en la presión del agua. Algunos fabricantes utilizan tecnología patentada para reducir esta caída de presión, que le sugerimos que investigue al seleccionar una bomba. Generalmente, si una bomba de 50 HP puede sostener un orificio de 0.014 «a una presión de operación continua de 60,000 psi, la implicación es que se habrá abordado este desafío de caída de presión hidráulica.
La Figura 14 muestra las fluctuaciones de presión en la línea de agua de alta presión antes del acumulador de presión. Esto muestra un cambio de presión de mayor a menor de casi 22.000 psi. Entonces, para un sistema de 60,000 psi, el agua a alta presión pasaría de 60,000 psi a 40,000 psi después de cada golpe del intensificador.
Si esta fluctuación de presión no fuera suavizada por el atenuador de presión, los resultados de corte en la pieza de trabajo serían indeseables. Habría una línea significativa en la parte con cada golpe del intensificador. Recuerde que cualquier cambio en la presión resulta en un cambio en la velocidad del chorro de agua en el cabezal de corte. Este cambio de velocidad cambia la velocidad a la que se mueven las partículas abrasivas y, por lo tanto, la cantidad de fuerza que impartirán sobre la pieza de trabajo. Una presión más baja conduce a una menor velocidad del agua, lo que conduce a una menor fuerza del abrasivo, lo que conduce a un corte más lento o una calidad de borde más áspera.
Afortunadamente, el atenuador de presión suaviza estos picos de presión para que el agua en el cabezal de corte mantenga una presión, velocidad y potencia de corte constantes.
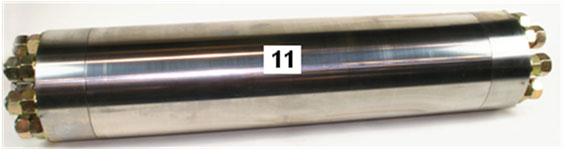
Figura 13 - Atenuador de presión
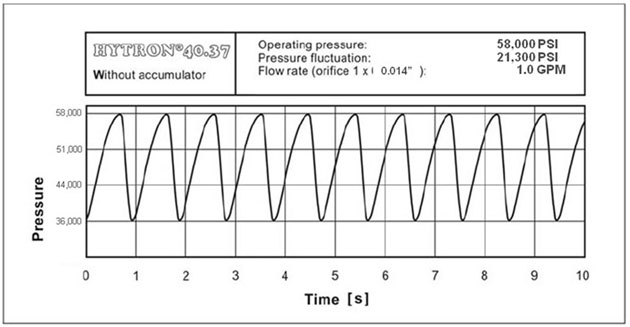
Figura 14 - Fluctuación de presión antes del acumulador
Fuente: "Fluctuaciones de presión y caudal en bombas intensificadoras de alta presión", F. Trieb, et.al., 2007 American WJTA Conference and Expo
12. Entrada de agua
Antes de ingresar al gabinete de la bomba, es posible que deba tratarse el agua para que el agua esté dentro de las especificaciones del fabricante del chorro de agua. Dentro del gabinete de la bomba, generalmente en la parte inferior, el agua generalmente pasará por uno o más filtros finales justo antes de ingresar al intensificador (número 12 en las Figuras 15 y 2).
El agua de entrada debe poder mantener un caudal y una presión especificados para garantizar que el intensificador reciba suficiente agua. El agua entrante también debe cumplir ciertos requisitos con respecto a los sólidos disueltos totales (TDS), el pH, la materia orgánica, la temperatura, etc. La mala calidad del agua resultará en una reducción drástica de la vida útil de los componentes de alta presión (es decir, cualquier cosa con la que entre en contacto el agua a alta presión). Los diferentes fabricantes de bombas requieren diferentes presiones de agua de entrada, algunos necesitan tan solo 30 psi y otros requieren una bomba de aumento de presión de agua para mantener 100 psi. La calidad del agua se discutirá con más detalle en el capítulo 4 «Calidad del agua».
Figura 15 - Filtros de agua de entrada
13. Controles y PLC
Los controles y el PLC (no se muestra en la imagen) controlan las válvulas en el circuito hidráulico para determinar la presión y el flujo de aceite hidráulico hacia y desde el intensificador. También se pueden integrar varios sensores e interruptores de proximidad en los controles para monitorear toda la bomba y verificar cosas como la velocidad de carrera, la temperatura y presión del aceite, la presión y el flujo de agua de entrada, y más. Esta capacidad facilita mucho el trabajo y la resolución de problemas con el intensificador de hoy en día.
La válvula neumática On-Off controla el flujo de agua al cabezal de corte. La válvula de encendido y apagado en el corte está «normalmente cerrada». Es decir, cuando no se suministra aire comprimido a la válvula On-Off, una aguja encaja firmemente contra un asiento para evitar que el agua a alta presión llegue al cabezal de corte. Cuando se suministra aire comprimido a la válvula de encendido y apagado (es decir, comando de «herramienta encendida» desde el control), la aguja se fuerza hacia arriba desde su ubicación de asiento y el agua a alta presión puede fluir a través del orificio hasta el cabezal de corte.
Dentro o cerca del gabinete de la bomba de alta presión hay otra válvula de encendido y apagado que funciona en conjunto con la válvula de encendido y apagado en el cabezal de corte. La válvula de encendido y apagado de la bomba se denomina típicamente válvula de alivio de seguridad. Esta válvula de alivio de seguridad en la bomba está «normalmente abierta». Esta válvula permanecerá abierta cuando no se le suministre aire. Cuando la válvula de encendido y apagado en el cabezal de corte se cierra (comando de «apagado de herramienta» por control o no hay energía en el sistema), la válvula de alivio de seguridad en la bomba se abrirá, aliviando toda la presión de agua de la tubería de alta presión. Cuando el control emite el comando «herramienta encendida», la válvula de alivio de seguridad se cierra para que toda el agua a alta presión vaya al cabezal de corte. Tenga en cuenta que no todos los fabricantes de bombas nuevas tienen la válvula de alivio de seguridad como estándar. Le recomendamos encarecidamente que pregunte al fabricante de su bomba si suministra este estándar y cuándo está activado. Nuevamente, algunos fabricantes de bombas solo activarán la válvula de seguridad cuando se presione un paro de emergencia; cuando la bomba se detiene, las líneas de alta presión todavía están presurizadas.
Ambas válvulas de encendido y apagado deben estar en buenas condiciones de funcionamiento para proteger contra la descarga accidental de agua a alta presión en el cabezal de corte que podría lesionar gravemente a alguien que trabaje en el cabezal de corte o cerca de él o en cualquiera de las líneas de alta presión. Se requiere el reemplazo periódico de la aguja, el asiento y las partes asociadas para mantener estas válvulas.
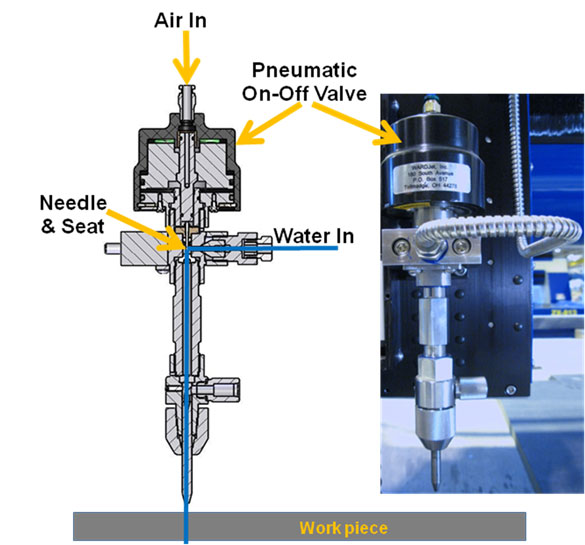
Sistema de alimentación de abrasivo
Tolva a granel presurizada
El abrasivo se transporta a través de tuberías y presión desde una gran tolva a granel ubicada cerca del sistema de corte por chorro de agua a una mini-tolva cerca del cabezal de corte. Las tolvas a granel normalmente contienen desde varios cientos de libras de abrasivo hasta 2200 libras. Si está cortando con una cabeza y 1,4 libras por minuto de abrasivo, entonces está consumiendo alrededor de 84 libras por hora. Una tolva de 1100 libras duraría unas 13 horas de funcionamiento. Esto significaría que la máquina podría funcionar durante más de un turno antes de que fuera necesario volver a llenarla. La mayoría de los chorros de agua cuentan con tolvas de aproximadamente 600 libras, lo que equivaldría a unas 7 horas de funcionamiento. Por lo tanto, al menos una vez durante un turno de 8 horas, la tolva deberá recargarse. Se deben evaluar los costos asociados con el tiempo de inactividad adicional en el transcurso de un año.
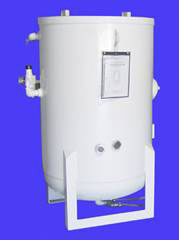
mini tolva
Por lo general, se monta una minitolva cerca y encima del cabezal de corte. La mayoría de estas minitolvas permiten la alimentación por gravedad del abrasivo hasta el cabezal de corte. Muchas minitolvas controlan la cantidad de abrasivo que puede bajar al cabezal de corte con el uso de una corredera con orificios de diferentes tamaños. El operador puede cambiar la posición de la corredera para cambiar la cantidad de abrasivo al cabezal de corte.
Un avance tecnológico reciente es el control CNC remoto de la cantidad de abrasivo liberado de la minitolva. Tener esta capacidad permite una alimentación óptima de abrasivo al cabezal de corte en relación con la presión del agua en la bomba para las siguientes capacidades deseables:
- Perforación de materiales frágiles como vidrio o piedra. Por lo general, se utilizará una presión de agua más baja con una cantidad menor de abrasivo
- Cambiar la cantidad de abrasivo para diferentes tamaños de boquilla abrasiva para optimizar el costo de la pieza. Esto se puede hacer automáticamente si la mini tolva está configurada para hacerlo.
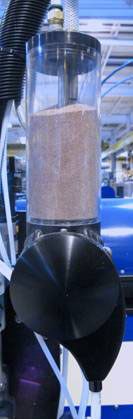
Resumen
En este capítulo, después de una breve revisión del proceso de corte por chorro de agua, analizamos los dos estilos diferentes de bombas que se utilizan en el corte por chorro de agua a alta presión: intensificador y accionamiento directo, y cubrimos algunas de las ventajas de cada estilo de bomba. Se detalló el proceso de presurización de agua de una bomba intensificadora. Revisamos las diferentes partes de una bomba intensificadora para que tenga una buena idea de lo que habla un vendedor o un técnico cuando se refiere a una parte de una bomba. También discutimos la válvula de encendido y apagado y cómo se usa en el cabezal de corte y en la bomba. Se discutió el sistema de alimentación de abrasivo, así como las ventajas de un sistema de dosificación de abrasivo controlado por CNC.
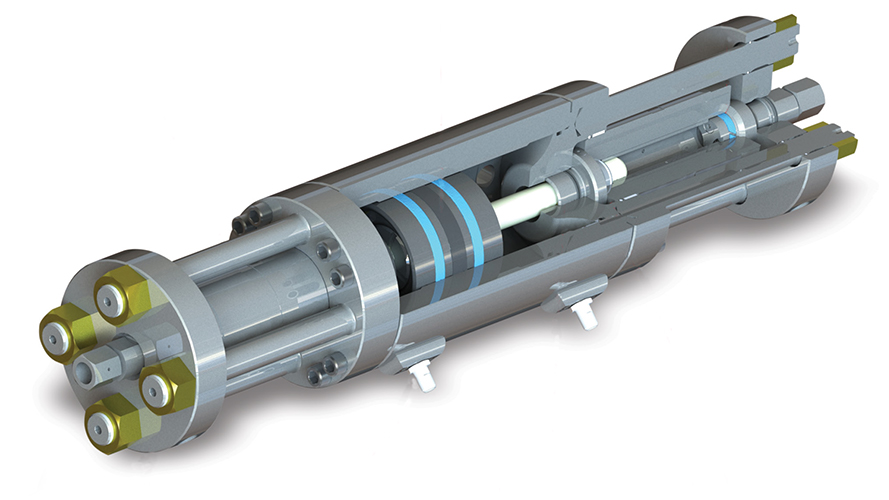














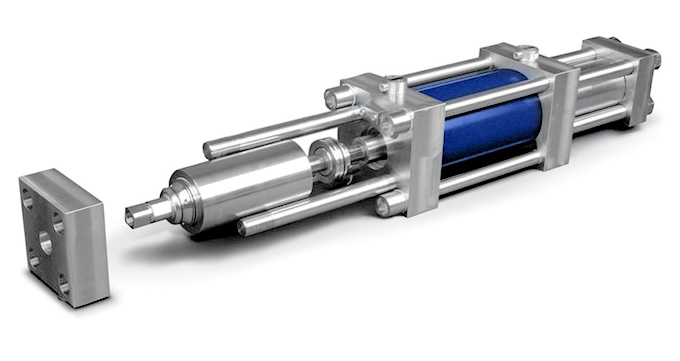












Ponerse en contacto
Unete a nuestro equipo
Siempre estamos buscando personas con conocimientos apasionados por brindar una experiencia excepcional al cliente. ¡Hablemos!